Keeping the Flow Going: The Vital Role of Cargo Pumps in Gas Carrier Vessels
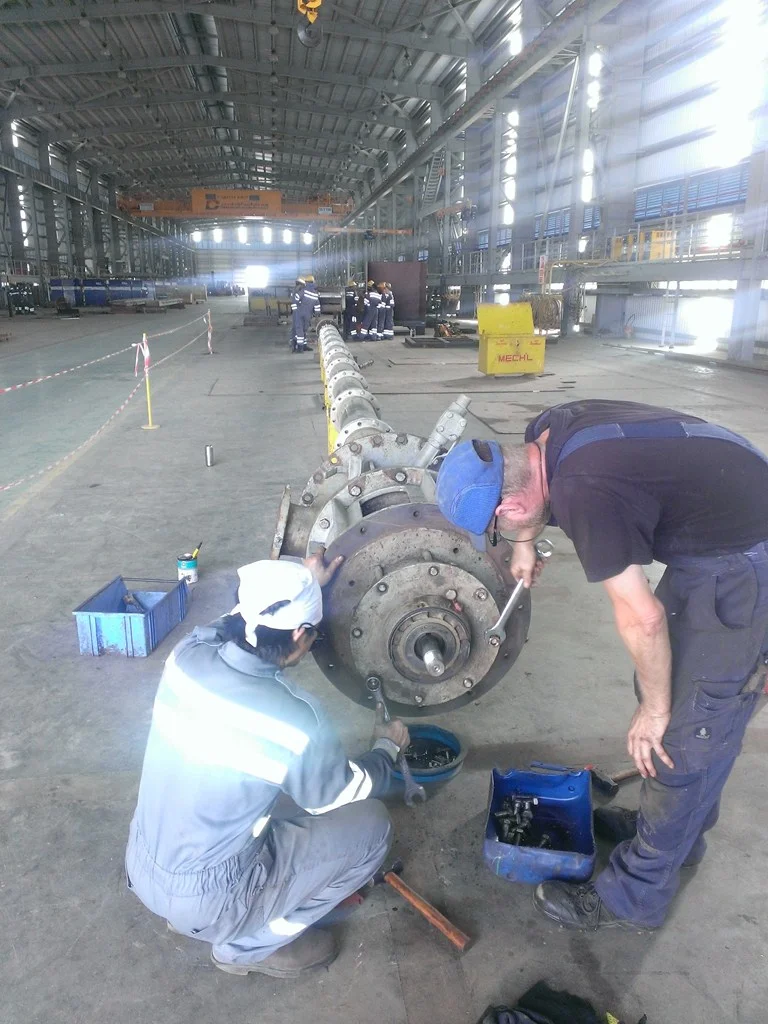
In a gas carrier vessel, cargo pumps and shafts are critical components of the cargo handling system. These systems are responsible for pumping liquefied gases such as LPG (liquefied petroleum gas) and LNG (liquefied natural gas) from the storage tanks to the discharge ports for delivery to customers.
The cargo pumps used in gas carrier vessels are typically centrifugal pumps, which use a rotating impeller to create a flow of fluid. These pumps are designed to handle the specific properties of liquefied gases, such as their low temperatures and high pressures, and are typically located in the cargo tanks themselves.
To ensure the safe and efficient transfer of liquefied gases, cargo pumps are often equipped with a range of safety features, including:
Pressure and temperature sensors to monitor the condition of the cargo and the pump.
Emergency shutdown systems that can quickly shut down the pump in the event of an emergency.
Anti-vibration systems to reduce the risk of damage to the pump or other equipment.
The cargo shaft is the component that connects the cargo pump to the electric motor that drives it. This shaft is typically made of high-strength materials such as stainless steel, and is designed to withstand the high stresses and pressures involved in pumping liquefied gases.
To ensure safe and reliable operation, cargo shafts are typically equipped with a range of safety features, including:
Bearings and seals to prevent leaks and reduce friction.
Monitoring systems to detect any signs of wear or damage.
Emergency shutdown systems that can quickly stop the pump in the event of a malfunction.
In summary, cargo pumps and shafts are critical components of the cargo handling system in gas carrier vessels. These systems must be designed and maintained to the highest standards to ensure the safe and efficient transfer of liquefied gases.
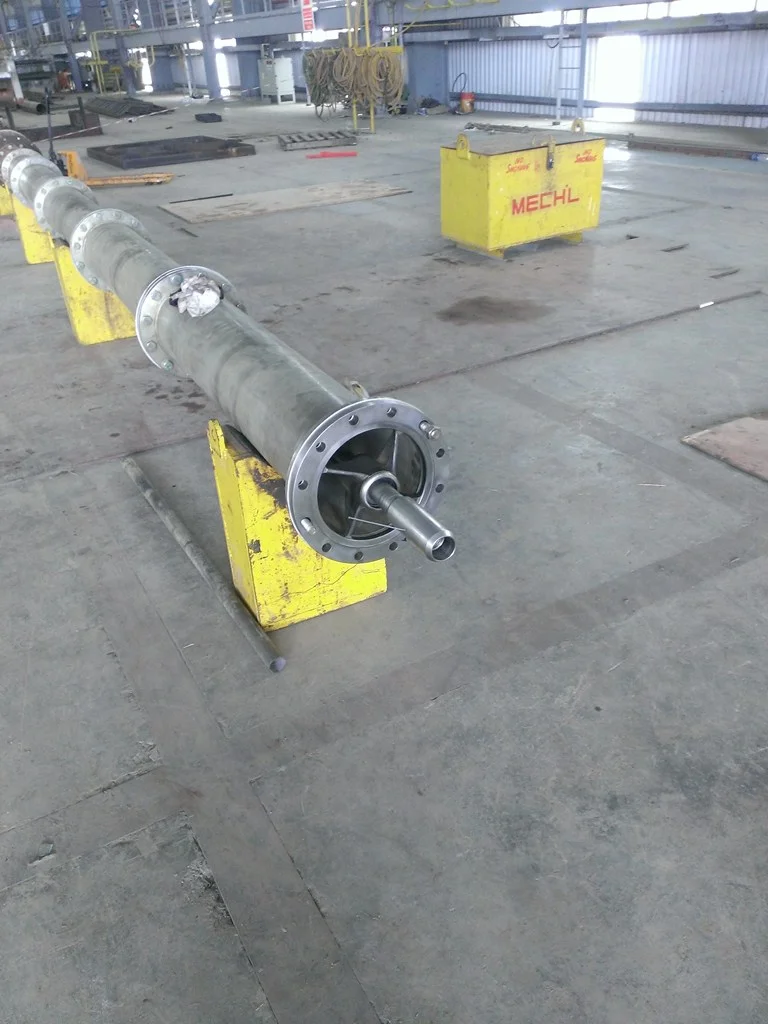
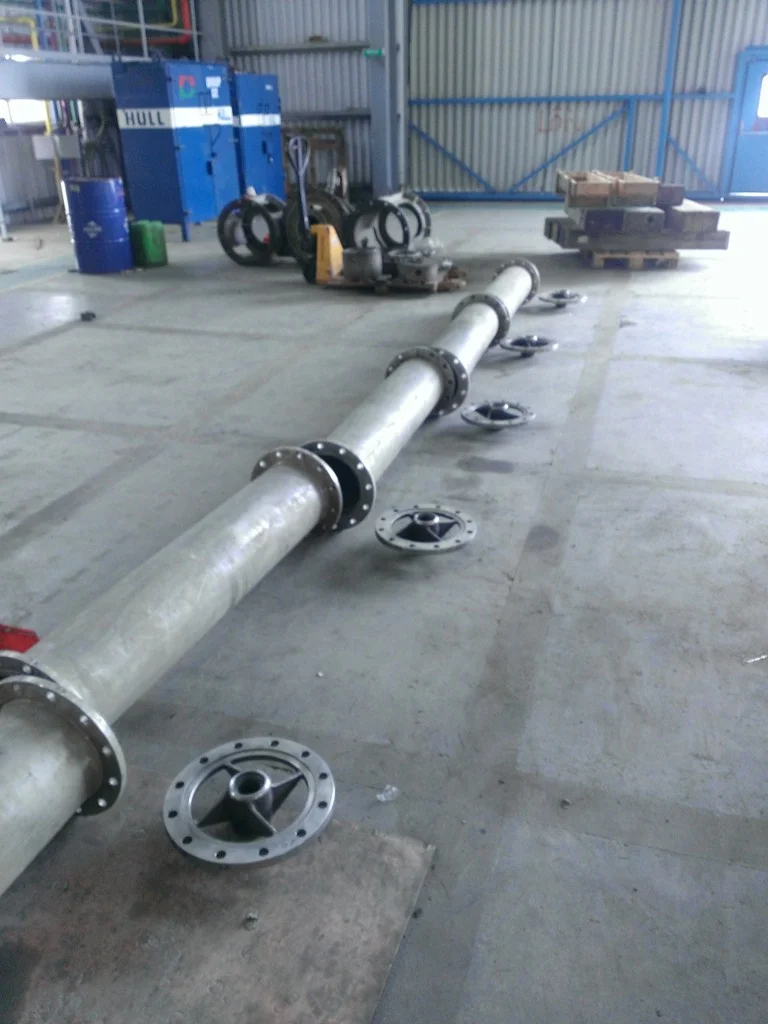
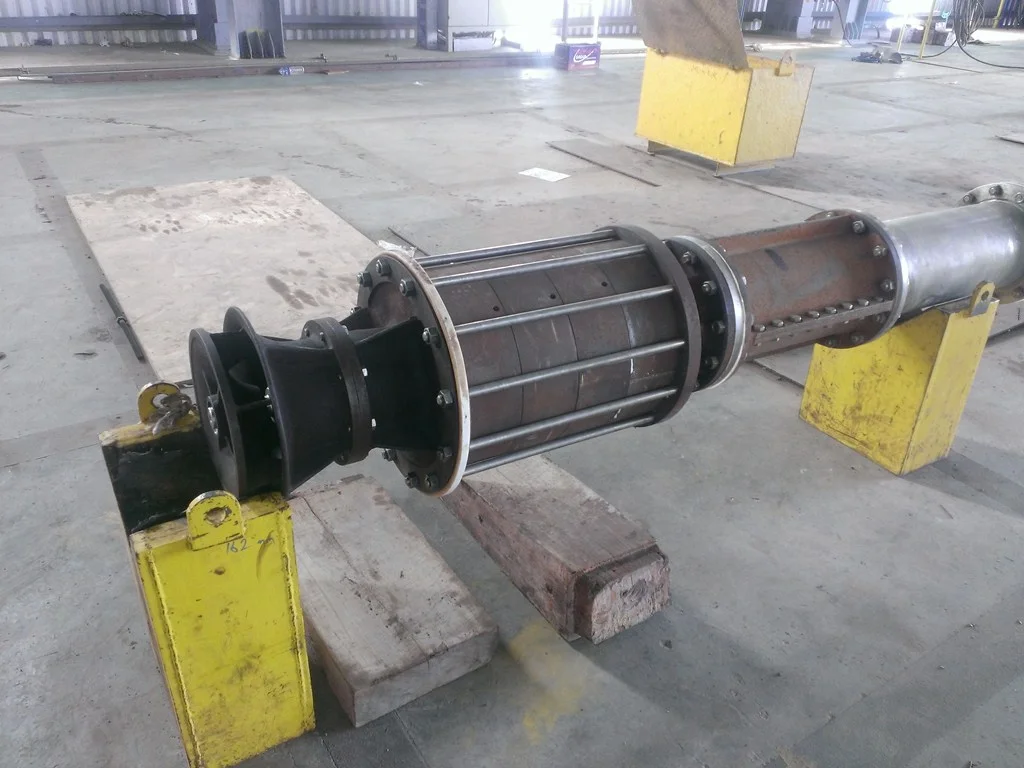