FSRU Managing Cargo Operations: Challenges and Lessons Learned
Floating Storage and Regasification Units (FSRUs) have revolutionized the liquefied natural gas (LNG) industry, providing flexible and cost-effective solutions for LNG importation and regasification. Despite their advantages, FSRU operations come with unique challenges that demand meticulous planning, robust systems, and operational excellence. This article highlights some of the key challenges faced in FSRU operations and shares valuable lessons learned.
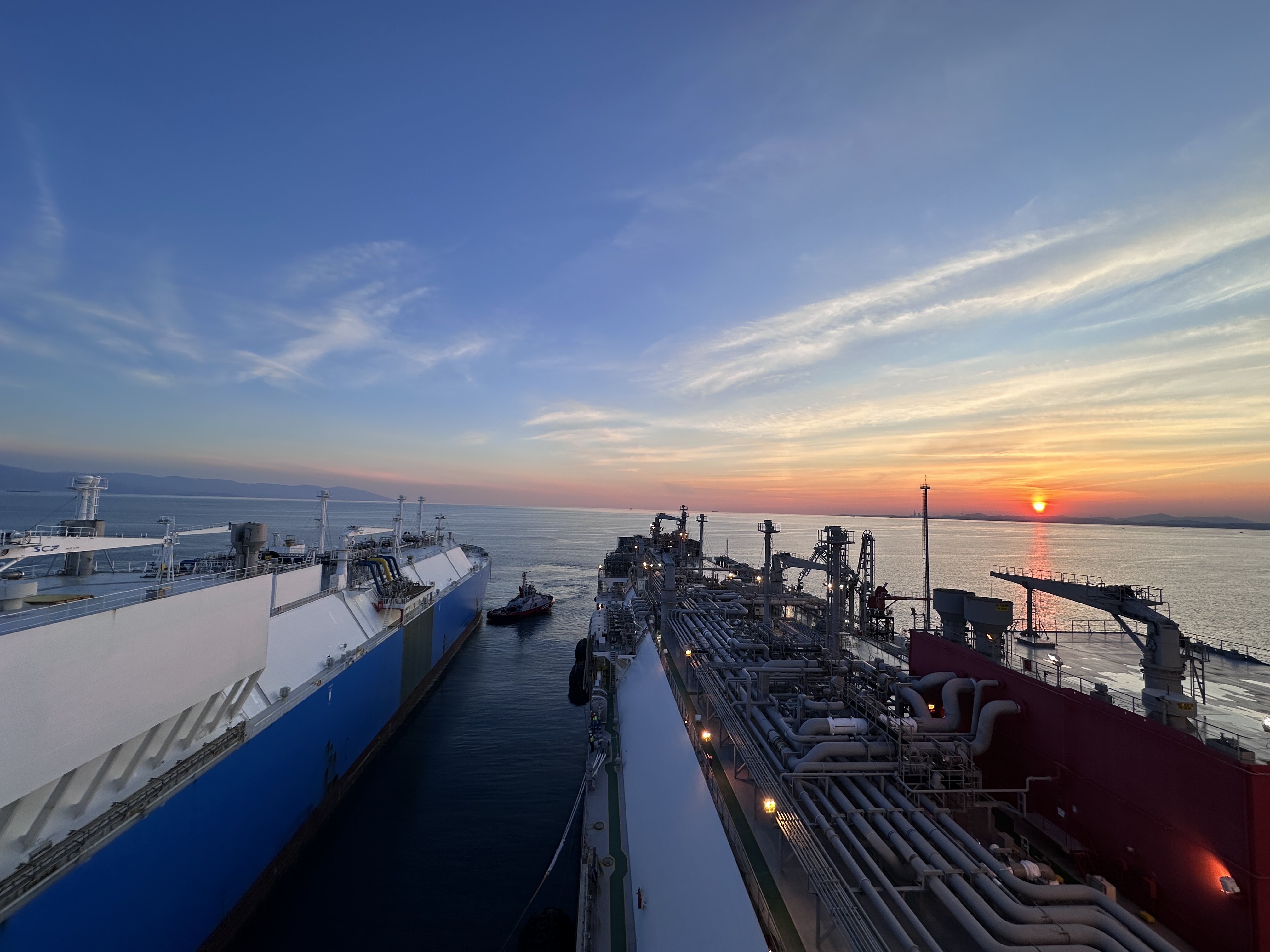
1. Liquid Line Cooldown
Challenges:
• Ensuring controlled cooldown rates to prevent thermal stress on cargo tanks and pipelines.
• Managing the transition from ambient temperatures to cryogenic conditions without exceeding safe cooldown rates.
Detailed Lessons Learned:
• Pre-Loading Cooldown Procedures: The liquid line cooldown should follow a systematic approach as described in the vessel manual. Initiate cooling with low-flow rates of LNG vapor to gradually reduce temperatures before introducing full flow.
• Automation and Monitoring: Advanced automation systems in the cargo control room should be utilized to monitor flow rates and temperature gradients. The Integrated Automation System (IAS) ensures precise regulation during this phase.
• Avoiding LNG Shock Loading: Thermal shock to tanks and pipelines can be minimized by maintaining strict adherence to cooldown timelines and pressure thresholds.
2. Ship-to-Ship (STS) Transfer Operations
Challenges:
• Handling the transfer of LNG between FSRU and LNG carriers, especially in adverse weather or during dynamic mooring conditions.
• Ensuring compatibility between the FSRU and the LNGC manifold systems.
Detailed Lessons Learned:
• Pre-Transfer Preparations: Conduct detailed compatibility checks, including manifold alignment, hose connection integrity, and communication protocols. The STS checklist from the vessel operational framework emphasizes these preparatory steps.
• Real-Time Monitoring: Utilize flow meters, pressure sensors, and in-line sampling systems to ensure steady flow and prevent over-pressurization during LNG transfer.
• Training for Dynamic Conditions: Crew training for handling dynamic mooring and quick-release mechanisms enhances safety and efficiency during transfers.
3. Rollover Prevention
Challenges:
• Preventing stratification within the cargo tanks, which can lead to density imbalances and potential “rollover” incidents.
• Managing tank pressures and boil-off gas (BOG) effectively during storage.
Detailed Lessons Learned:
• Cargo Mixing: Employ tank circulation pumps to ensure uniform temperature and density within the cargo. This prevents the formation of stratified layers that can trigger rollovers.
• Tank Monitoring Systems: Continuous monitoring of pressure, temperature, and density gradients using radar gauges and tank level sensors is critical. These systems are integrated into the control room displays.
• Preventive Actions: Any sign of stratification should trigger immediate recirculation and pressure equalization measures guided by operational checklists and alarms from the IAS.
4. Gas Sampling and Analysis
Challenges:
• Ensuring the purity and quality of LNG during cargo transfer and storage.
• Maintaining accurate records for custody transfer agreements.
Detailed Lessons Learned:
• In-Line Gas Sampling Systems: Use dedicated vaporizer probes for real-time sampling. The high-pressure natural gas manifold system on the vessel is equipped with state-of-the-art gas analyzers to verify LNG quality during transfer.
• Custody Transfer System (CTS): The radar-based CTS ensures precise measurements of LNG volume and density, enabling accurate billing and preventing disputes with charterers or suppliers.
5. Emergency Shutdown (ESD) Procedures
Challenges:
• Coordinating rapid shutdown of cargo operations during emergencies like hose ruptures, excessive pressure build-up, or equipment failure.
Detailed Lessons Learned:
• Multi-Level ESD System: The FSRU employs a tiered ESD system to ensure staged shutdowns, minimizing risks to personnel and equipment.
• Regular Drills: Simulated drills for cargo transfer emergencies help the crew respond promptly to real scenarios, ensuring effective use of ESD systems.
6. Boil-Off Gas (BOG) Management
Challenges:
• Controlling the accumulation of BOG in storage tanks, particularly during holding or low-demand periods.
Detailed Lessons Learned:
• Recondensers and Gas Compression: Utilize onboard recondenser systems to liquefy excess BOG and return it to the storage tanks. This is a key feature of the FSRU cargo handling system.
• Parallel MSO Operation: Deploying multiple MSOs (Main Send-Out compressors) in tandem enhances the flexibility of BOG handling during peak and idle phases.