Boil-Off Gas (BOG): The Key to Unlocking Efficiency in FSRUs
Boil-off gas (BOG) management is a critical aspect of FSRU operations, directly impacting efficiency, safety, and environmental compliance.
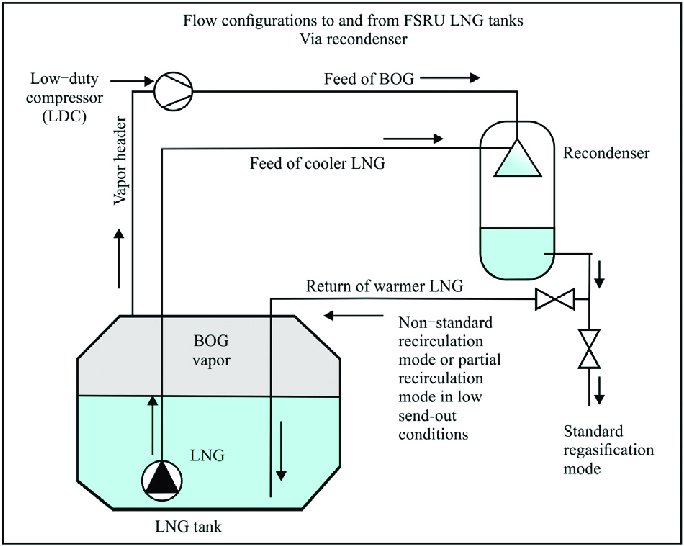
Challenges in BOG Management
1. Continuous Generation of BOG:
• LNG stored at cryogenic temperatures (-162°C) in tanks is subject to heat ingress, causing constant evaporation (boil-off gas).
• During high-demand periods, regasification typically consumes BOG, but managing it during low-demand or idle phases is challenging.
2. Excess BOG During Holding Mode:
• When the regasification system is inactive or operating below capacity, excess BOG accumulates in cargo tanks, creating pressure build-up.
3. Environmental Concerns:
• Venting BOG to the atmosphere is not only wasteful but also harmful to the environment, given its contribution to greenhouse gas emissions.
4. Equipment and System Constraints:
• Recirculation systems, compressors, and recondenser units must operate efficiently to handle varying volumes of BOG without causing system overloads.
Detailed Strategies for BOG Management
A. Recondenser Utilization
Process:
• Excess BOG is directed into the recondenser, where it is mixed with incoming LNG. This process re-liquefies the gas, converting it back into LNG for storage.
Benefits:
• Prevents the need to vent BOG into the atmosphere, conserving valuable LNG and reducing emissions.
• Maintains tank pressure within safe operating limits.
Application on FSRU
• The recondenser system is integrated with high-pressure booster pumps and vaporizer units to ensure continuous operation during fluctuating demand.
B. Forced BOG Burning
Process:
• During holding mode or low-demand periods, BOG can be burned in dual-fuel engines or gas combustion units (GCUs).
Advantages:
• Reduces tank pressure effectively.
• Utilizes BOG as a fuel source, contributing to power generation on board.
Key Considerations:
• Monitoring the calorific value of BOG and ensuring compatibility with engines or GCUs to avoid operational inefficiencies.
C. Parallel MSO (Main Send-Out Compressor) Operation
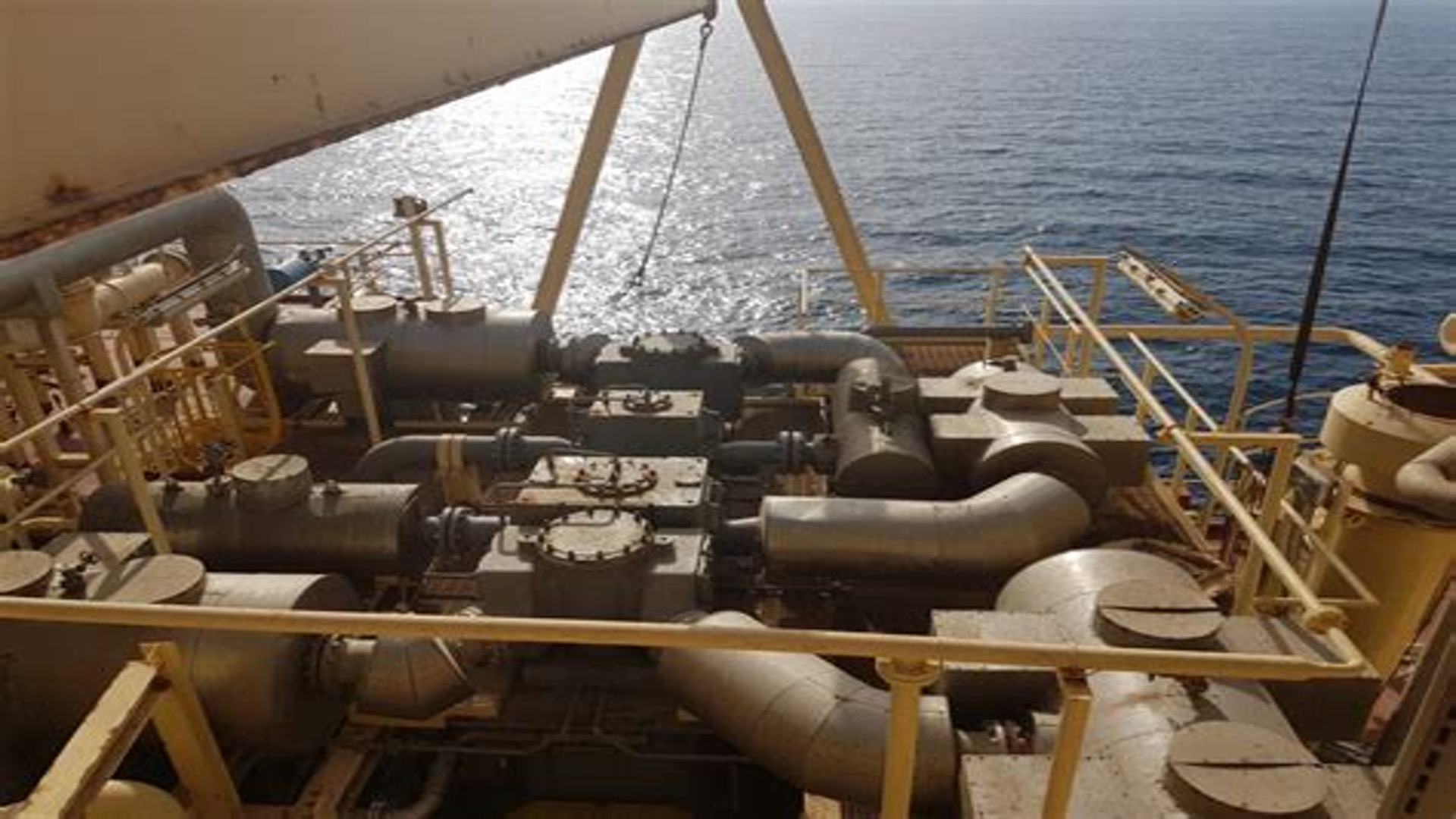
Process:
• Running multiple compressors in parallel helps manage varying volumes of BOG efficiently.
Benefits:
• Ensures redundancy; if one compressor fails, others can handle the load.
• Maintains stable pressure and flow during peak and idle periods.
Application:
• The MSO system on FSRU is designed to handle both steady-state and fluctuating demands, ensuring seamless integration with regasification systems .
D. Holding Mode Operations
Normal Boil-Off Gas Burning:
• During regular operations, natural boil-off gas (NBOG) is burned in engines or used in auxiliary systems.
Forced Boil-Off Gas:
• Excessive gas during extended holding periods is deliberately generated and burned to maintain tank integrity.
System Integration:
• The IAS ensures that the forced BOG burning process is automated, reducing the risk of manual errors and improving efficiency .
E. Monitoring and Control Systems
Pressure and Temperature Monitoring:
• The cargo control room on FSRU is equipped with advanced monitoring systems to track tank pressure and temperature in real time. Alerts are triggered if parameters exceed predefined limits.
Automation:
• Integrated control systems automatically adjust recondensation, compression, or burning processes based on real-time data, ensuring optimal BOG handling at all times.
F. Environmental Compliance
Emission Control:
• Using gas combustion units (GCUs) ensures that any vented BOG is burned off safely, converting methane into less harmful CO₂ and water vapor.
Regulatory Adherence:
• Systems are designed to meet IMO and local environmental regulations, minimizing greenhouse gas emissions during FSRU operations.
Lessons Learned
1. Proactive System Maintenance:
• Regular inspection and maintenance of recondenser units, compressors, and vaporizer systems ensure smooth BOG handling and prevent unexpected failures.
2. Crew Training:
• Crew members must be thoroughly trained in BOG management systems, including emergency protocols for high-pressure situations.
3. System Redundancy:
• Incorporating redundancy in compressors and GCUs minimizes the risk of downtime and ensures continuous operation, even during equipment failure.
4. Real-Time Data Utilization:
• Leveraging automation and real-time monitoring systems improves decision-making and ensures efficient BOG management under varying operational scenarios.
Conclusion
Effective BOG management is essential for the operational efficiency and environmental sustainability of FSRUs. By employing advanced systems such as recondensers, GCUs, and automation, operators can mitigate the challenges of excess BOG while conserving energy and adhering to environmental standards. These strategies not only optimize operational performance but also position FSRUs as a greener alternative in the LNG supply chain.